The VIC-3D Educational (EDU) System is a low-cost solution developed for academic institutions to assist in teaching the Digital Image Correlation technique to undergraduate and graduate students. The VIC-3D EDU system utilizes the same accurate DIC algorithms found in the powerful VIC-3D software, while allowing users to acquire data quickly and easily. The system features a simplified setup, streamlined image acquisition, and ideal post-processing features. The stereo cameras are mounted inside a protective enclosure, which includes an integrated LED light source, a cooling fan, and an exterior USB & power connectors. The system also includes a tripod, tripod head, speckle roller, ink pad, calibration target, and a convenient carrying case.
- ‹ Previous
- 1
- …
- 4
- 5
- 6
Feature Product
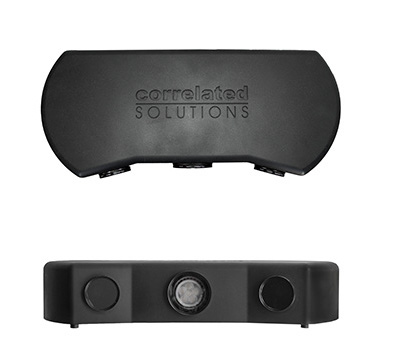
he VIC Educational System (VIC-EDU) is a low-cost solution developed for academic institutions to assist in teaching the Digital Image Correlation technique to undergraduate and graduate students.
View Product